Are there more customer demands today for higher levels of storage and more sophisticated material distribution?
Yes, today's modern warehouses are not just about racks and forklifts, they are now home to increasingly sophisticated automated solutions and more sophisticated handling technology. A concrete insight into smart warehousing is provided by our Modula automated vertical system, which is one of the "smart" warehousing solutions using WMS Premium software. This addresses not only what is in an automated warehouse, but also the safety of goods, maximises capacity on minimal floor space, saves space and time in operations, increases efficiency, reduces risk and links the software to the ERP for full communication.
How will AMR and IGV (Intelligent Guided Vehicles) apply in the logistics environment?
Automated handling technologies represent a very broad field that is developing rapidly. Until now, this technology required human operators, but this is no longer entirely true. More and more machines are moving between shelves without human intervention and performing a range of activities based on instructions from the warehouse system, either alone or in cooperation with humans. The advent of object-handling robots represents in some ways the pinnacle of warehouse automation, but a new era of collaborative robot proliferation is dawning.
Our Agilox autonomous handling technology allows you to transport goods based on warehouse or production requirements. They drive safely past people during autonomous operation, and cooperate with people during other operations.
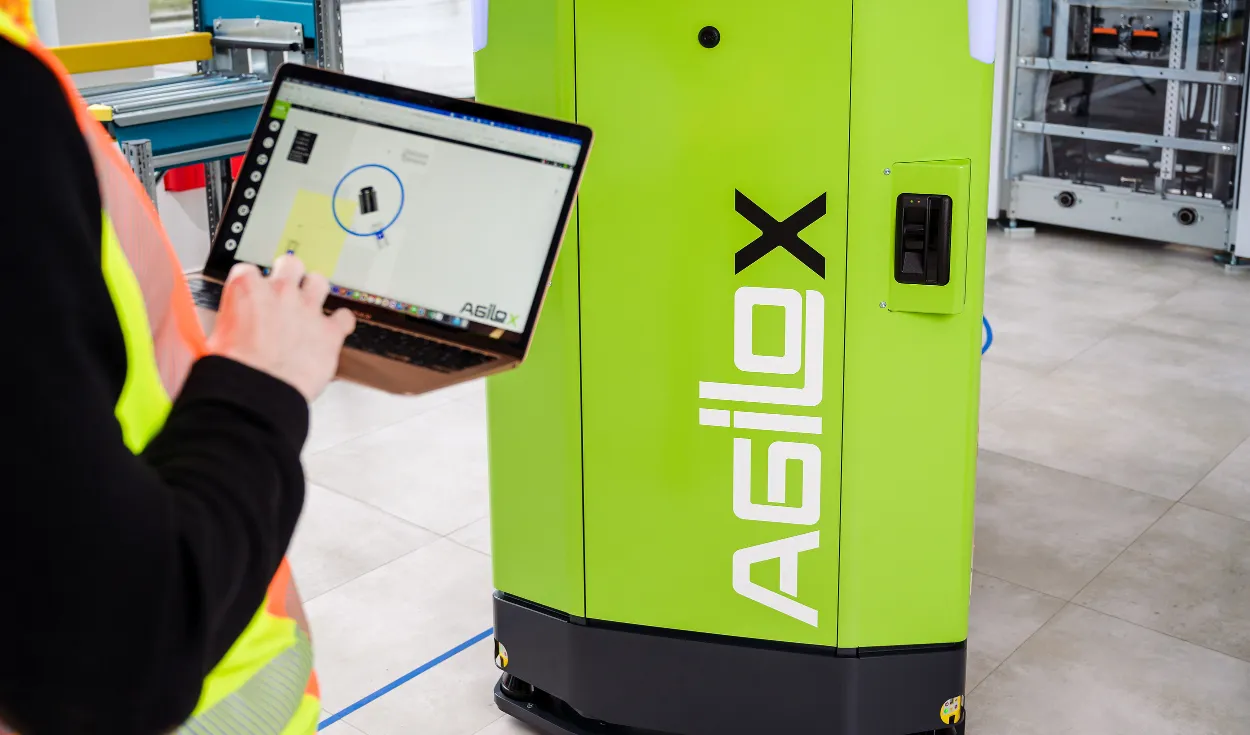
Robotics is all about people, experts in programming, maintenance, etc. Each software is specific in some way, for example, how quickly a robot can decide to complete a task as quickly as possible. For example, the IGV Agilox navigates using maps stored in its memory and has omnidirectional wheels, allowing it to turn on the spot. It doesn't need headlights, markers on the walls or on the ground - it uses the X-Swarm software platform application for all-round flexibility.
For example, when production workers need to deliver material from a warehouse, they call up Agilox using a PDA device and a barcode or other code that contains the information needed for the autonomous truck to locate the material in the warehouse. The robot automatically loads the material from a pre-determined position using the overhead system and delivers it to the production line. Thanks to safety sensors, the entire operation is very safe for other employees.
Which direction will the future development take?
When humans and robots work together, new possibilities open up for managing their cooperation. Combined processes make it possible to address the issue of interchangeability. For example, if a situation arises that is difficult for a human to handle, the robot will handle it and vice versa. However, in the case of combined human-robot systems, safety issues must also be addressed as a priority.
Thanks to our intelligent Swarm Agilox system, the first AMR vehicle can be integrated into the production environment with commissioning in less than twelve hours, and each additional vehicle in just 15 minutes. This means that Agilox can be relocated for temporary use in other divisions or branches of the company. Commissioning can also be handled by company personnel.
What challenges do you have to "tackle" and what has the new facility brought?
We often encounter the fact that production and logistics do not work in cooperation because production is dealt with first and logistics second. Many times there is a contradiction. That is what we are trying to change in order to find a consensus that meets both environmental requirements. Implementing such a robotic environment and working with people requires a certain level of understanding. This is also made possible by the sophisticated X-Swarm software technology. Orders are transmitted via WLAN directly to the IGV or AMR, which then divides the orders between them. Depending on a number of parameters, it decides autonomously which vehicle will accept the order. The aim is to ensure that each route is transported in a cost- and time-optimised manner.
Ambient data from all transport systems is used to determine the optimal route. Thanks to the integrated Swarm intelligence in the vehicles, there is no need to outsource work to higher-level systems. It is therefore possible to monitor parking space occupancy using sensor technology and automatically trigger supply commands.
- Dušan Šutka, published in TECHMAGAZINE magazine