Vitesco Technologies Czech Republic is currently implementing the Agilox autonomous handling technology from our company 4IGV. The company is planning a number of system solutions in the field of storage and transport. One of the plans is, for example, automatic scanning of goods immediately on receipt. We spoke with Petr Sodomka, head of logistics at the Trutnov plant of Vitesco Technologies Czech Republic.
Could you please first briefly introduce your logistics? What do you do here and how?
In terms of personnel, the logistics department at the Trutnov plant consists of approximately 140 colleagues. Approximately half of this number are office workers. Our logistics includes four main areas. The first of these is physical logistics, i.e. all warehouse management - receiving, dispatching, supplying materials to production sites, etc. Another important area of our logistics is packaging management. We focus both on the development of packaging, which not every company does on its own, and also on taking care of the running of packaging, i.e. its distribution from us to our suppliers, as well as the administration and distribution of packaging from customers to us. In cooperation with an external partner, we also do the cleaning of the packaging. The third part of our logistics is project logistics. This includes all the agenda related to process improvement and logistics reporting. The fourth part is layout logistics, where we include, for example, production planning, the planning of material deliveries from suppliers and the agenda of communication towards customers.
Can you reveal your latest innovations in internal logistics?
We are currently completing the project to launch our first autonomous Agilox truck from 4IGV. The trucks of this brand are already running in some of our foreign plants. In our company in Trutnov, this is the first full-fledged implementation of an autonomous trolley in the true sense of the word. There are already partial applications in the Czech Republic, for example in production, but a high level of interaction with humans is still needed. Here, the operation of the trolley will be fully autonomous, the machine will be independent of humans.
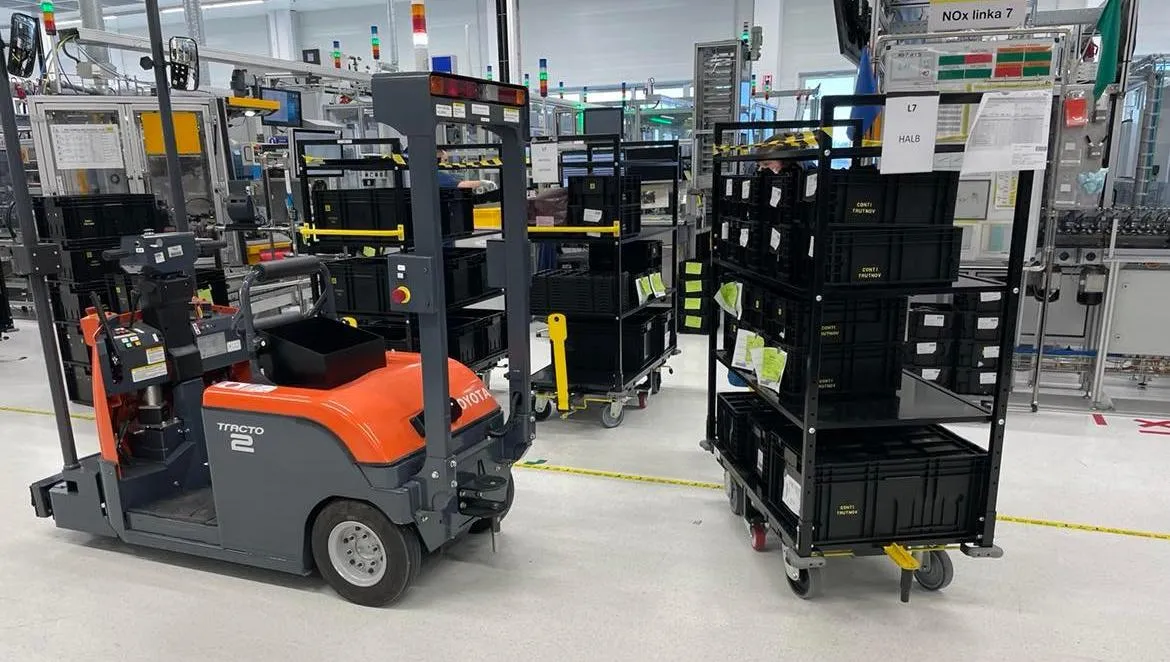
What will be the task of this truck?
He will operate dedicated production sites. Production workers will assemble the pallet and place it in the designated location. As the truck passes by, it will detect itself using scanning technology to pick up the pallet and transfer it to a delivery point in the warehouse. All this will happen without human intervention. As soon as the warehouseman sees that the autonomous handling technology has brought a pallet from the factory, a human will intervene and will have to load the pallet into the main warehouse. That's where our automation doesn't reach yet. We see this as one of our ambitious goals for the future. The Agilox truck will therefore be tasked with picking up pallets of finished products and bringing them to the warehouse, as well as loading the packaging for the final products back into production. This keeps the machine busy in both directions.
On what basis does this autonomous technology receive commands?
We have not yet fully connected this technique to the WMS system. In the future, we are considering linking it to our SAP system as well. At the moment, the idea is that the machine can recognize that a pallet with finished products has appeared at a defined location. This in itself is an incentive for it to pick it up and take it to the warehouse. This had to be preceded by an accurate mapping of the positions.
Are you considering purchasing more autonomous vehicles?
Yes, we are. We have identified several other locations within other production departments where this application makes sense. Generally speaking, Agilox trucks are worthwhile wherever uniform pallets are transported, i.e. wherever pallet-by-pallet handling takes place. At the same time, there is a distance criterion to be met for which autonomous technology is worth using. In general, the greater the distance over which the pallet is transported by the trolley, the more the application makes sense. The third prerequisite for autonomous technology is the creation of a stable surrounding environment. In practice, this means good layout discipline. Once we say that autonomous technology will go from point A to point B, we have to make sure that this is respected, that the material to be transported is actually on the pallet at the designated location. Furthermore, the places through which the technology passes must meet certain parameters in terms of occupational safety.

In lean logistics, I often see logistics trains, i.e. tractors and trailers. Many logistics trains are now automated. Was this not an option for you?
It was. We even implemented our first logistics train last year. You make a nice point about the potential of milkruns. It's true that even this technology doesn't have to be completely dependent on humans anymore. The technology that we have acquired and that is running in our country allows us to go into semi-automated mode in the future. We have a rig from Toyota Material Handling CZ. Today it is operated by a driver, a so-called train driver. On the other hand, once the process has stabilised and we think we are ready to take the next step, milkrun allows us to program the stopping routes in advance. So we can send it out and it will know exactly which line to stop at so that the workers can take the appropriate volume of goods. Conversely, a final production cart can be hitched to the train for transport to the warehouse. There is no one-size-fits-all solution to meet all logistics requirements, so it has to be the ideal mix of what delivers the greatest efficiency.
Do you see the automation of intralogistics as a significant trend?
Automation is a significant trend. In our intralogistics company, we are gradually jumping on the automation bandwagon. We are rather at the beginning, on the other hand: I don't think this is a bad thing. In logistics, even more than in production processes, it is true: measure twice and cut once. You first need to think carefully about how much automation makes sense in a particular process. The payback itself also needs to be considered very well. It is only when it is clear that automation makes sense in all aspects that it is worth investing in. I am convinced that it pays to be conservative, to introduce automation gradually, because you can always get faster. Automation projects tend to be costly, at the same time costing a lot of effort from the whole team, so everything needs to be thought through first, evaluated and then implemented.
Do you have any vision for the future in this regard? What would you like to see?
We have a freshly completed long-term strategy in which we see five years ahead. Within the strategy, we take into account all our processes and have identified potential within them. We have put each of the potential projects in context over time so that we are able to plan our investments well. We are allocating resources within the teams to do this incrementally, so that we are able to properly grasp each project and see it through to completion.
What does the actual storage look like in your plant?
Much of this takes place in conventional racking systems, which are operated by system stackers, i.e. system trolleys. These are manually controlled. We do not rule out automation in this area in the future either. The goods on pallets are transported to the vicinity of the system trolleys, where the pallets are removed and stacked. The opposite is the case for picking from the racks. Unloading is carried out according to production requirements.
Which direction will you take next?
We will certainly not resist any good and appropriate Industry 4.0 solutions. It's not just about autonomous vehicles, we have a whole range of ideas. For example, we are starting to talk about a project for automated scanning of goods as soon as they come to us from our suppliers. Today, the loading is done manually by our staff, each packing unit is scanned into the system. We are looking at scanner technology that could scan goods as soon as they are unloaded from the truck. The system's receipt would then be done automatically. This has a lot of potential, but it has a few "buts" so far. One of those "buts" is that we need to improve the discipline of our suppliers in the area of marking. For example, suppliers would have to ensure the quality of the labelling, the placement of the labels and the correct composition of the pallet so that the label is always clearly visible.
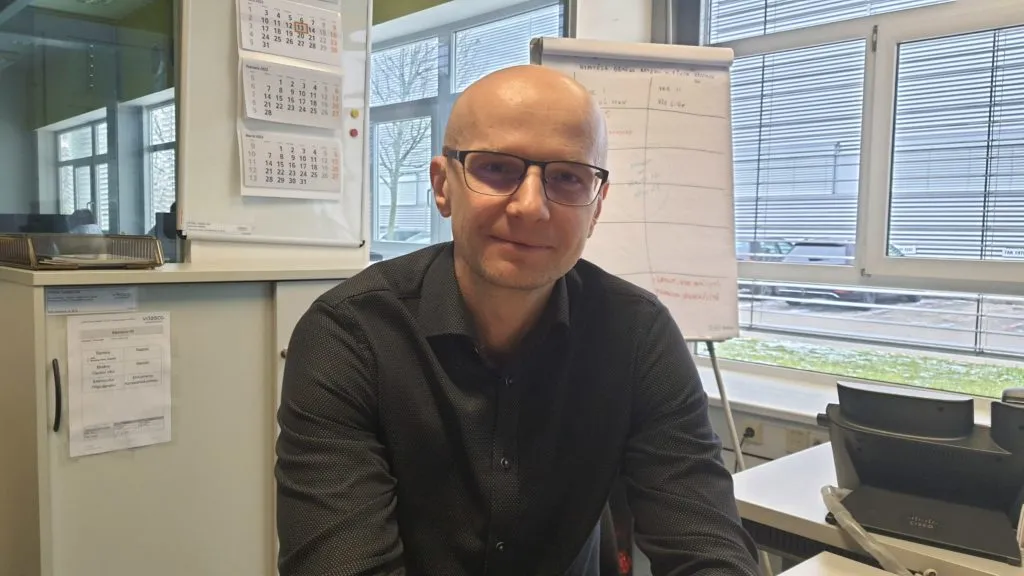
This would certainly place great demands on system work with data...
But that is exactly the future of logistics. Software can make the work in logistics much easier, but it must always be a conceptual solution. We are thinking about getting an application that would consolidate our transport planning and registration issues in one place. Following on from this, we would also like to solve the issue of efficient planning and use of ramps. In practice, we can imagine that whoever wants to come to our ramp, for example a supplier to unload materials or a customer to load products, we will be able to plan these arrivals and loadings online.
The loading windows could be efficiently stacked one behind the other to avoid overloading or, on the contrary, to avoid unnecessary "deaf" spots. In the future, we are considering a system extension that would allow us to control incoming and outgoing traffic throughout our plant. The advantage of this technology is that it can make downstream processes much more efficient. Last but not least, it will allow us to collect data so that we can evaluate everything on an ongoing basis.
- interview by Petr Neckař, photo: author's archive and Vitesco Technologies